As the world looks toward renewable energy to achieve zero-carbon energy solutions, hydrogen power is poised to displace environmentally harmful fuel sources and toxic battery banks. However, ensuring this transition is seamless and widely adopted requires a reduction in current material costs.
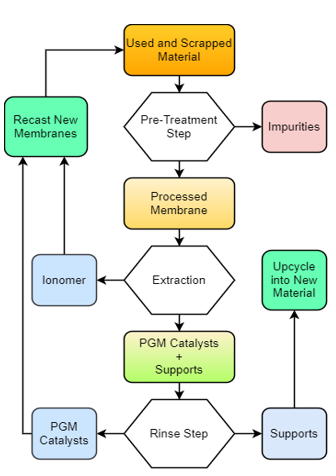
In this project, Tetramer is establishing routes to recycle the two active components of hydrogen fuel cells and electrolyzers – membranes and platinum group metal (PGM) catalysts. These materials are expensive to produce, and decommissioned devices are difficult to dispose of; but recycling efforts promise a chance to rescue materials at the end of their life cycle and close the manufacturing loop – preventing waste, increasing supply, and driving down costs.
This approach will turn otherwise hazardous waste into an economic opportunity, yielding new jobs and bolstering the sustainability and affordability of a much-needed green technology.
Tetramer Research Scientist Matt Wasilewski said, “Leveraging our team’s considerable membrane R&D expertise, Tetramer is uniquely suited to the development of recovery and recycling techniques for these membranes and catalysts. We look forward to the successful completion of Phase I efforts demonstrating the feasibility of extraction and ensuring recovery can be achieved with minimal cost and waste. In Phase II, we plan to develop additional routes for recovering valuable materials as well as recycling paths for membrane components such as supports, additives, or fillers.”
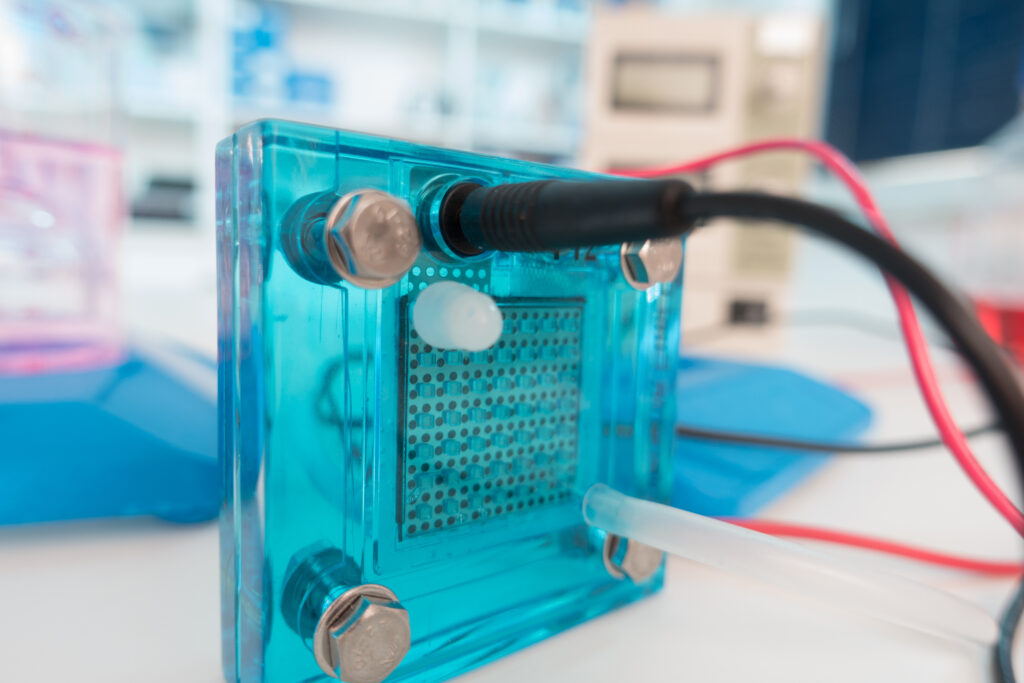
Tetramer scientists have been active leaders in the development of membranes for hydrogen fuel cells, water vapor transport, electrolyzers, and solar fuels generators for the last 15+ years.
Learn more about the Tetramer Membranes Program and ongoing projects here.
Public Project Summary: “Sustainable Recovery of Fuel Cell and Electrolyzer Materials”
Phase I DE-FOA-0002903, Topic C56-11a
Problem Being Addressed: Renewable energy sources are experiencing a surge of growth due to rising power demand but suffer asynchronous production relative to societal needs. To balance the overproduction during low demand and underproduction during high demand, proton exchange membrane (PEM) based electrolyzers (capable of producing zero-carbon, green hydrogen) and fuel cells (for clean electricity generation and zero emission transportation) are utilized. Fully embracing this technology will require lowering the cost of these devices, currently hindered by expensive commercial PEM materials and platinum group metal (PGM) catalysts. Recycling efforts can lower the cost, but current means rely on incineration to recover the PGMs, producing hazardous byproducts and destroying the valuable PEM. More efficient and environmentally benign processes are necessary.
Approach to Solving Problem: This Phase I work will focus specifically on assessing the feasibility of several approaches that extract both the PEM and PGM component from scrap and spent membranes. This approach will use mild treatments to recover components intact with less energetic or destructive processes. Promising routes with be further developed during Phase II as will recycling paths for other components of membranes, such as supports, additives or fillers.
Phase I Approach: Specific approaches which will be assessed during Phase I are (i) minimal-solvent, low waste extraction, (ii) azeotropic mixture rinses designed to extract maximum amounts of PEM which can be easily recovered themselves and (iii) agitation/hot soaking techniques in non-hazardous solutions. In all cases the PGM catalyst recovery will be enhanced by capturing larger particles rather than recovering nanoparticles from soot by smelting or corrosive acids.
Commercial Applications and Other Benefits: Beneficial outcomes include: (i) a profound reduction in energy costs and expense of clean hydrogen; (ii) increased domestic PGM metal supply security, and (iii) a reduction of persistent fluorinated waste entering the environment from incineration of PEM or by their disposal into landfills from the perfluorosulfonic acid (PFSA) components of PEMs.
Member of Congress Summary: Proton exchange membranes are essential technology for producing renewable, clean hydrogen. Recycling the components will lower energy costs, increase domestic supply security regarding rare platinum group metals and lessen the environmental burden associated with disposing of persistent, long lived fluorinated wastes.
Key Words: Fuel Cell, Electrolyzer, Proton Exchange Membrane, Hydrogen, non-perfluorosulfonic acid (non-PFSA), Clean Energy, Zero Carbon