Partnering with Universities
Provide your email address in the form below to receive updates on potential collaborations with Tetramer on SBIR / STTR topics of interest.
Partnering with Universities
Tetramer Technologies is seeking university collaborators interested in advancing and commercializing technologies from their labs through the Small Business Innovation Research (SBIR) and Small Technology Transfer Innovation Research (STTR) programs. SBIR/STTR programs advance high risk, high reward technologies to commercialization by providing funding for entrepreneurship activity. During an SBIR/STTR, a university collaborator can use funds to provide research opportunities for undergraduates, graduates, and post docs. Successful commercialization can result in potential royalty streams for inventors and universities and new jobs for students.
Tetramer has extensive background in contracting and executing these programs and in partnering with universities through the process. We are working to identify university partners with good technical fit from a concept and capabilities perspective.
Submit your contact information below to receive updates on future collaboration opportunities.
Email addresses will be used ONLY for this purpose and sent only a few times per year when funding opportunity announcements are released.
If you are interested in collaborating with Tetramer on any of the below topics of interest, please reach out to the contact listed below each topic of interest and include a non-proprietary quad chart of your proposed idea. Be sure to indicate research capabilities information (i.e. equipment, experience, etc.) and whether there is existing IP.
Download Quad Chart Template Here (PowerPoint File)
The Tetramer lead for each topic will review requests and coordinate meetings with researchers as appropriate.
Current Topics of Interest: Army STTR Phase I 24.B and DOD 24.2 SBIR
Contact the Tetramer PI listed by May 10, 2024
Final proposals due 6/12/2024
DOD 24.2 SBIR Topics
N242-070 Hydrogen Generation Salt-water Electrolysis with Chemical Compression
Tetramer POC: Chris Topping, PhD (chris.topping@tetramer.com)
OUSD (R&E) CRITICAL TECHNOLOGY AREA(S): Advanced Materials; Renewable Energy
Generation and Storage
OBJECTIVE: Develop a hydrogen generation system that uses salt water to produce one to five kg of
hydrogen over a 24-hour period in an austere environment. All components of the system shall be stored,
transported, and operated in quad-con ISO containers. The system shall be required to leverage Onboard
Vehicle Power (OVP), currently fielded tactical generators, and alternative power sources (e.g., solar or
mobile nuclear power generation).
DESCRIPTION: As part of its future force modernization efforts, the Marine Corps seeks to deploy
small, disaggregated hydrogen generation units to foreign locations where access to energy sources will
be limited or unavailable. These units are to specifically support the U.S. Marine Corps’ Expeditionary
Advanced Base Operations (EABO), a form of expeditionary warfare that involves the employment of
mobile, low-signature, naval expeditionary forces that operate from a series of austere, temporary
locations.
N242-082 Selective Stripping of Cadmium and Zinc-Nickel Coatings
Tetramer POC: Monika Mujkic, PhD (monika.mujkic@tetramer.com)
OUSD (R&E) CRITICAL TECHNOLOGY AREA(S): Advanced Materials; Sustainment
OBJECTIVE: Develop a method for selectively stripping cadmium (Cd) and zinc-nickel (Zn-Ni) coatings
from small areas (i.e., several square inches/centimeters) on high-strength steel components, without
generating dusts that pose an inhalation risk.
DESCRIPTION: Cadmium (Cd) coatings and Zn-Ni coatings are used on many high-strength steel
components on aircraft, such as landing gear assemblies on fixed-wing aircraft and the rotor masts of
rotary aircraft. These coatings prevent corrosion and protect the integrity of the underlying steel.
However, over time as the coating gets damaged or worn, the coating must be removed and repaired.
For parts that are overhauled at the depot level (D-level), spent Cd or Zn-Ni coatings can be stripped by
immersing the part in a chemical tank. After the coatings are stripped, the underlying metal can be
inspected, repaired as necessary, and then recoated with fresh Cd or Zn-Ni coatings. Depot level facilities
have chemical processing plants that allow for this type of work to be performed safely.
However, this chemical process is not feasible to perform at intermediate (I-level) or organizational (Olevel)
level maintenance facilities. Dozens of I-level and O-level facilities around the world perform
touch-up repairs of Cd or Zn-Ni coatings on aircraft components, often to fix localized damage that
requires stripping and recoating several square inches (centimeters) of surface area. To remove the old
coating when a chemical processing plant is not available, maintainers use methods such as hand sanding,
wet sanding, or abrasive blasting to abrade away the Cd or Zn-Ni layer. Unlike with full immersion in a
chemical processing tank, using abrasive methods to remove coatings generate inhalation and exposure
risks to the maintainer, as well as to the surrounding environment. Particularly with Cd coatings, Cd is
carcinogenic and long-term exposure can increase the risk of various cancers and other health effects.
There have also been cases where maintainers use an incorrect abrasive that is too aggressive,
inadvertently causing damage to the component they are processing. This results in increased rework
costs and delays in returning the component to the fleet.
This SBIR topic seeks a method for stripping Cd and Zn-Ni coatings that generate no inhalation exposure
risks for maintainers, eliminates the possibility of Cd dust release into the maintenance hangar or
surrounding environment, and a method that is repeatable and easy for maintainers to use with no risk of
causing inadvertent damage. An ideal solution should be able to remove both Cd and Zn-Ni coatings, be
simple and cost-effective, and be easy to deploy to I-level and O-level maintenance sites around the
world. The method must selectively strip Cd and Zn-Ni coatings without damaging other coating types,
such as primers and topcoats. The method must also not damage the underlying steel component, such as
through corrosion or hydrogen embrittlement.
N242-089 Alternative Fabrication Pathways for Complex Alloys
Tetramer POC: Stephen Hudson, PhD (stephen.hudson@tetramer.com)
OUSD (R&E) CRITICAL TECHNOLOGY AREA(S): Advanced Materials; Hypersonics;Sustainment
OBJECTIVE: Develop a solid state processing pathway to fabricate refractory high entropy alloys that
avoids partitioning (in multi-phase Alloys) seen in melting/solidification processes.
DESCRIPTION: Refractory high-entropy alloys (RHEAs) are considered a new kind of high-temperature
materials with great application prospects due to their excellent mechanical properties and have the
potential to replace nickel-based superalloy as the next generation of high-temperature materials for gas
turbine and hypersonic applications. Currently, the majority of methods for processing of Cantor (3d
transition) HEAs and metallic RHEAs are melt derived. This process can be challenging due to the
disparate and extremely high melting points of the constituent metals. Moreover, elemental segregation
often occurs during the solidification process, resulting in compositional inhomogeneity. In multi-phase
alloys, portioning of elements into different phases occurs. This elemental partitioning promotes diverse
properties in the different phases of the alloys such differing passivity properties. This SBIR topic seeks
to develop a method for Cantor and RHEA production based on the reduction of a mixture of metal
oxides, or a mixture of oxides and metallic powders. Processes utilizing non-flammable gas mixtures
would be advantageous. The process could be aimed at obtaining (1) RHEA metallic powders (for
subsequent solid-state processing) or (2) RHEA bodies (via additive processing of ceramic powders and
subsequent reduction heat-treatment). Examples of target RHEAs compositions include MoNbTaW and
HfNbTaTiZr.
N242-094 Anti-Corrosion Coating for Gas Turbine Compressor Components Operating in Marine Environments
Tetramer POC: Stephen Hudson, PhD (stephen.hudson@tetramer.com)
OUSD (R&E) CRITICAL TECHNOLOGY AREA(S): Sustainment
OBJECTIVE: Develop and demonstrate a chemically and mechanically robust coating system or other
surface treatment for sustained protection of engine compressor components, such as mating compressor
stages, cases, and vane tracks, from corrosion in naval aero engine operation.
DESCRIPTION: In naval aviation, aircraft operate in and around marine atmospheric environments often
with high humidity and salt content, which accelerates corrosion degradation of aircraft components.
High compressor operation temperatures relative to ambient conditions create a cyclic environment within
the engine, in which water can evaporate and cool between flight and ground time cycles, leading to the
accumulation of salts and other contaminants. This cyclic environment further accelerates corrosion
mechanisms. As a consequence of this cyclic, marine atmospheric environment, multiple components
throughout military aircraft propulsion systems require frequent repair and/or replacement due to severe
corrosion and pitting, which leads to high maintenance costs, increased engine removals, and reduced
aircraft readiness.
The Department of the Navy is seeking the development and/or demonstration of a coating system or
other surface treatment for sustained protection of compressor components from corrosion in naval aero
engine operation. Such a proposed solution must have the mechanical durability to provide corrosion
protection along surfaces in contact and under some loading from other components. Specific components
of concern are low-pressure and high-pressure compressor stages and cases and are typically composed of
martensitic stainless steels (17-4PH and Jethete M152), titanium (Ti-6Al-4V), and Inconels (IN600,
IN718, IN909) [Note: specific alloys will be identified upon project award]. Proposed solutions may
constitute either the development of a new solution or a demonstration leveraging an existing solution in
naval aviation application.
AF242-0009 Graphene CBRN Overgarment
Tetramer POC: Heather Lange (heather.lange@tetramer.com)
OUSD (R&E) CRITICAL TECHNOLOGY AREA(S): Emerging Threat Reduction; Mission Readiness
& Disaster Preparedness; Nuclear; Sustainment & Logistics; Military Infectious Diseases
The technology within this topic is restricted under the International Traffic in Arms Regulation (ITAR),
22 CFR Parts 120-130, which controls the export and import of defense-related material and services,
including export of sensitive technical data, or the Export Administration Regulation (EAR), 15 CFR
Parts 730-774, which controls dual use items. Offerors must disclose any proposed use of foreign
nationals (FNs), their country(ies) of origin, the type of visa or work permit possessed, and the statement
of work (SOW) tasks intended for accomplishment by the FN(s) in accordance with the Announcement.
Offerors are advised foreign nationals proposed to perform on this topic may be restricted due to the
technical data under US Export Control Laws.
OBJECTIVE: By using Graphene, provide a two-part CBRN Protective overgarment with the first part
protecting the wearer from most if not all CBRN agents while reducing the weight and thermal load of the
overgarment. The second part will be using Graphene to create ballistic plating up to level III+ while
weighing a fraction of what current level III+ plates (roughly between 4-11 pounds). With the reduced
weight it would allow the wearer to don more protective pieces to areas such as the arms, legs, and other
body parts.
DESCRIPTION: Results of breakthrough times for the Graphene suit against CBRN agents and compare
them to the current protective overgarment as well as comparing the results to Level B and Level A
Chemical suits used in HAZMAT.
Ballistic test results for the lighter weight level III+ plates showing that the Graphene plates can meet or
exceed the standard of current plates.
AF242-D018 Development of Advanced Surface Treatments for Astroquartz Fibers
Tetramer POC: Adam Haldeman (adam.haldeman@tetramer.com)
OUSD (R&E) CRITICAL TECHNOLOGY AREA(S): Advanced Materials
The technology within this topic is restricted under the International Traffic in Arms Regulation (ITAR),
22 CFR Parts 120-130, which controls the export and import of defense-related material and services,
including export of sensitive technical data, or the Export Administration Regulation (EAR), 15 CFR
Parts 730-774, which controls dual use items. Offerors must disclose any proposed use of foreign
nationals (FNs), their country(ies) of origin, the type of visa or work permit possessed, and the statement
of work (SOW) tasks intended for accomplishment by the FN(s) in accordance with the Announcement.
Offerors are advised foreign nationals proposed to perform on this topic may be restricted due to the
technical data under US Export Control Laws.
OBJECTIVE: The objective of this project is to develop advanced coupling agents and surface treatments
for Astroquartz fibers in order to increase the environmental and thermal durability of various Polymer
Matrix Composite systems, which include a range of resin matrices from 350 degree Fahrenheit-curing
epoxies to advanced polyimides.
DESCRIPTION: Astroquartz-reinforced Polymer Matrix Composites (PMCs) are widely utilized on
aircraft in radome applications due to excellent dielectric properties compared to other variants of glass
and carbon fiber reinforcements. Although the mechanical performance requirements for these
applications are not as demanding as other structural PMC components that utilize carbon fiber
reinforcement, the environmental and thermal durability can limit their service life and significantly
impact maintainability. Recent testing performed on various PMC systems with resin matrices ranging
from 350 degree Fahrenheit-curing epoxies to advanced polyimides have exhibited extensive disbonds at
the fiber-matrix interface after moisture and thermal conditioning. The objective of this project is to
develop advanced coupling agents and surface treatments for Astroquartz fibers in order to increase the
environmental and thermal durability of various Polymer Matrix Composite systems of interest. This
SBIR should seek to identify key contributing factors for the limited durability in PMC systems of
interest, develop optimized surface treatment processes for woven Astroquartz reinforcements, and
develop tailored coupling agents that offer increased durability over the current state-of-the-art systems.
SF242-0018 Neon recovery and reliquefication for low temperature characterization of infrared focal plane arrays
Tetramer POC: Bogdan Zdyrko, PhD (bogdan.zdyrko@tetramer.com)
OUSD (R&E) CRITICAL TECHNOLOGY AREA(S): Space Technology
The technology within this topic is restricted under the International Traffic in Arms Regulation (ITAR),
22 CFR Parts 120-130, which controls the export and import of defense-related material and services,
including export of sensitive technical data, or the Export Administration Regulation (EAR), 15 CFR
Parts 730-774, which controls dual use items. Offerors must disclose any proposed use of foreign
nationals (FNs), their country(ies) of origin, the type of visa or work permit possessed, and the statement
of work (SOW) tasks intended for accomplishment by the FN(s) in accordance with the Announcement.
Offerors are advised foreign nationals proposed to perform on this topic may be restricted due to the
technical data under US Export Control Laws.
OBJECTIVE: The primary objective is to develop commercial products that specifically permit infrared
detector characterization lab users to recover, purify and reliquefy neon gas, at the small scale (<10 liters
per day of liquid neon), back into a cryogenic liquid intended for use in pour fill cryogenic dewars, and,
thereby, reducing the burden of acquiring additional liquid neon.
DESCRIPTION: Characterizing infrared focal plane arrays is ideally done with the test part in a pour fill
dewar that uses liquid cryogens, rather than a closed-cycle system which potentially contributes noise to
the test system and limits ones ability to perform focal plane array characterization at a remote facility
such as a radiation source. Liquid neon is a near ideal liquid cryogen for this role. It boils at 27.5 K,
which is well below liquid nitrogen and, more specifically, below where typical high performance
infrared sensors operate, including long wave infrared detectors. Liquid neon also has over 40 times the
refrigerant capacity per unit volume than liquid helium.[1] During a detector characterization, these two
properties translate into fewer liquid cryogen transfers into the dewar using liquid neon, leaving more
time for characterization. This is an absolutely indispensable advantage in the highly unique circumstance
of a remote focal plane array radiation tolerance experiment, where access to the radiation source is
strictly limited, rarely available and expensive, and the part must be kept cold for over a week at a time.
Unfortunately, due to some unusual circumstances, liquid neon is very expensive and difficult to come by.
This is because 70% of the neon produced in the world is used in the growing semiconductor chip
manufacturing industry, where argon-flourine-neon excimer pulsed lasers are the workhorse source for
deep ultraviolet lithography and the ultra-high purity neon (~99.9999%) used in them must be replenished
every two weeks. Additionally, neon production occurs mainly as a byproduct of nitrogen generation via
cryogenic distillation of air, a technique that happened to be perfected in the Ukraine where grain
production requires large amounts of nitrogen for fertilizer. Given the current difficulties in the Ukraine
and its diminished production capacity and the growing use of neon in semiconductor manufacturing, the
price of liquid neon has risen to roughly $3000/liter, a 600% increase since 2014. Furthermore, there is
currently a single domestic distributor of liquid neon, Linde Corp. However, there is a straightforward
path to alleviating some of the hardship associated with the use of liquid neon for characterizing focal
plane arrays.
The technology to recover and liquefy certain gases, such as helium, at the small scale (~25 liters per day)
has been commercially available for nearly a decade and has had a major impact on research and medical
institutions ability to experiment, or run their instruments, at cryogenic temperatures. For example,
Quantum Design North America, located in San Diego, CA, already offers a complete line of helium
liquifiers and helium recovery, storage and purification systems, which allows users to recover and
liquefy the exhausted helium gas currently being lost from the normal boil off and helium transfers to
cryogenic instruments.[2] This technology alleviates the user’s dependence on cryogen suppliers and
lessens the impact of rising costs and undependable supply, as well as helps preserve a precious natural
resource which is vital to scientific research and medical treatment. With some modification, a similar
approach can now likely be adopted for the small scale (<10 liters per day) recovery and reliquefication of
neon used in scientific research. In fact, reliquefication of exhausted neon gas was already demonstrated
at the laboratory scale (~3 liters per day) in the early 1990s, but the technique was never adopted, likely
due to cost and availability of liquid neon.[3]
DHA242-003 Hydrogel-based Drug Delivery Product(s) for Traumatic Brain Injury
Tetramer POC: Heather Lange (heather.lange@tetramer.com)
OUSD (R&E) CRITICAL TECHNOLOGY AREA(S): Combat Casualty Care
OBJECTIVE: To develop and validate a biodegradable hydrogel drug delivery system for open-skull
fracture or penetrating traumatic brain injury (TBI) designed to seal the wounded environment and
facilitate the controlled, continuous release of hemostatic agents to stop intracerebral hemorrhage,
antimicrobials to prevent infection, and drugs to prevent brain swelling and herniation.
DESCRIPTION: Traumatic brain injury (TBI) is a significant health issue affecting military service
members during both wartime and peacetime. Care for TBI will be particularly challenging for military
medics as it will extend over a prolonged period, in far-forward, austere settings. Yet, this prehospital
phase of care is vitally important as the first link in the chain to prevent death and to limit secondary
injuries for TBI combatants. Currently, no therapeutic intervention is available as neuroprotective
treatment for TBI. In the battlefield, supportive measures usually include restoration of blood pressure
and tissue oxygenation through resuscitation or control of intracranial hypertension with hypotonic saline.
However, all these measures require skilled paramedics and reasonable medical settings, which are often
not feasible during combat. Future improvement in combat casualty outcomes depends on closing the gap
in prehospital care. One approach is to develop therapeutic products that can be readily available for
administrating by a Combat Medic and/or self or buddy-administration to mitigate morbidity and
mortality from TBI during prolonged field and enroute care.
Hydrogels are stable, highly malleable, and easily transportable matrixes that can potentially carry
multiple therapeutics. They are easy to apply and offer a promising solution for the point-of-injury care
for TBI. Moreover, they are ideal for extended release of drugs directly at the site of injury, bypassing the
systemic route and thus limiting potential adverse effects (Fernandez-Serra, Gallego, Lozano, &
Gonzalez-Nieto, 2020; Ma et al., 2020). The desired end-product would be a combination (biologic +
drug) therapy product utilizing an FDA-approved biodegradable hydrogel combined with an FDAapproved
drug that has demonstrated significant evidence of therapeutic benefit in the preclinical TBI
literature. The product target should be for TBI patients presenting with skull fracture or penetrating
wounds to the brain. This system should be designed to seal the wounded environment and facilitate the
controlled, continuous release of individual or multiple therapeutics including antimicrobials to prevent
infection, antioxidants, and anti-inflammatory drugs to prevent cellular damage, brain swelling, and
herniation. The release of the drug(s) should be unidirectional, facilitating drug infusion into the injured
tissue while mitigating any seepage into re-sutured skin and/or gauze bandages. A successful awardee
will design, develop, and demonstrate the utility of a hydrogel-embedded drug formulation for TBI in preclinical
studies.
Army 24.B STTR Topics
A24B-T004 Metamaterials Based on Magnetic Shape Anisotropy for K-band Microwave Applications
Objective: Develop a metamaterial utilizing magnetic shape anisotropy of ferromagnetic nanoparticles for operation of ultracompact antenna in the K frequency band of the microwave spectrum.
Description: Metamaterials demonstrating resonant response to electromagnetic radiation in the microwave Ku (12 GHz to 18 GHz) and K (18 GHz to 26.5 GHz) bands are highly desirable for multiple applications, including ultracompact microwave antennae, radar detection and frequency-selective wireless heating. Availability of ferromagnetic materials with high saturation magnetization and low magnetic damping [1,2], combined with recent advances in nanolithography, enable the development of such metamaterials based on arrays of ferromagnetic nanoparticles, where the resonance frequency of the metamaterial is determined by the magnetic shape anisotropy of the nanoparticles [3]. The shape anisotropy enables fabrication of devices with a selection of operation frequencies via lithography. For example, arrays of ultracompact antennae covering a wide band of the microwave spectrum, where each antenna is tuned to its own resonance frequency via control of the fabricated nanoparticle shape, can be used for ultrafast monitoring of the electromagnetic environment. An important advantage of a magnetic metamaterial is independence of its resonance frequency on the antennae dimensions [4], which enables ultracompact antennae for communications with miniature devices. The metamaterial antenna gain can be further boosted via magneto-electric or magneto-resistive effects in nanoparticle-based heterostructures to reach record levels of sensitivity to microwave signals [5].
The goal of this proposal is development of magnetic metamaterials based on arrays of ferromagnetic nanoparticles that show resonant response to electromagnetic radiation tunable by the nanoparticle shape. The metamaterial must operate at room temperature without a bias magnetic field and must show tunability of its frequency via shape anisotropy in the 2 GHz – 26.5 GHz frequency range (covering S, C, X, Ku and K bands). The metamaterial must exhibit resonant response to the frequency of incident electromagnetic radiation with the quality factor exceeding 100. To enable commercial applications, the metamaterial must be fabricated from a polycrystalline or amorphous ferromagnetic film deposited at room temperature by a high-throughput technique such as sputtering or electrodeposition. Operation of a K-band ultra-compact microwave antenna based on the shape-anisotropy metamaterial must be demonstrated. The overall antenna dimensions must not exceed 5 millimeters.
Interested in A24B-T004 Metamaterials Based on Magnetic Shape Anisotropy for K-band Microwave Applications? Contact Dr. Bogdan Zdyrko (bogdan.zdyrko@tetramer.com)
A24B-T014 Phase Change Materials for Enhanced Warfighter Survivability
Objective: The Army seeks innovative solutions utilizing phase change materials tailored for thermal regulation within a Closed-Circuit Self-Contained Breathing Apparatus to reduce thermal burden, enhance operational longevity, and improve warfighter efficiency.
Description: This STTR topic addresses the need for an advanced material solution capable of thermally regulating the microclimate of a Closed-Circuit Self-Contained Breathing Apparatus (CC-SCBA) by acting as a heat exchanger within the system. The envisioned technology would utilize phase change materials (PCMs) that are lightweight, reusable, and regenerative, with a transition temperature tailored to the unique operational demands of tactical respiratory protection devices.
Current CC-SCBA systems place a significant thermal load on the operator, leading to increased fatigue and reduced mission duration and effectiveness. Additionally, the inherent heat generation compromises the CO2 scrubbing efficiency, curtailing system endurance. The integration of an optimized PCM matrix could surmount these limitations by regulating the temperature of inspired air, thereby enhancing warfighter lethality and survivability.
The material must demonstrate efficacy in a composite or blend format, ensuring compatibility with existing CC-SCBA configurations and surpassing the performance of conventional ice-based systems. The developed technology should demonstrate structural stability and efficient thermal exchange within the constrained form factor of CC-SCBA units. Overall, success is defined by a phase change material that extends the operating lifetime of a CC-SCBA in terms of the thermal limitations set forth by the current NIOSH standard for CC-SCBAs (42 CFR 84.103). The ideal solution is a phase change material that can maintain an inspired air temperature below 35 °C under operational flow conditions for a duration of 4 or more hours.
The development process will include the optimization of encapsulation methods to prevent leakage and enhance material integration within the CC-SCBA framework. Additionally, these materials should exhibit long-term chemical stability and resistance to thermal degradation over repeated use cycles, ensuring reliability and safety in field operations. It should also be noted that the PCM will be required to operate in nearly 100% humidity in most normal conditions.
Interested in A24B-T014 Phase Change Materials for Enhanced Warfighter Survivability? Contact Dr. Bogdan Zdyrko (bogdan.zdyrko@tetramer.com)
A24B-T015 Distributed Multithreat Microsensor
Objective: Demonstrate a mission-configurable miniature, deployable sensing capability.
Description: Maneuver elements require early warning and situational understanding of the battlespace to include adversary actions and the threat of area denial tactics through the employment of hazardous persistent chemical agents. Soldiers are at risk of encountering dangerous circumstances as a consequence of having limited remote sensing capabilities for these situations. The joint forces require a small, lightweight technology that integrates with their equipment in a small form factor while affording prompt detection and reporting of the presence of multiple possible hazards or adversary troops and equipment in order to effect risk-based maneuver decisions and avoid hazards.
Emerging technology in miniature sensor science has increasingly demonstrated functionality and performance in the detection of hazardous chemicals and adversary movements and actions. Functionalized materials including metal oxide frameworks, carbon nanotubes, graphene, and conductive polymers have been reported with increasing sensitivity, selectivity, and reliability as environmental sensing modalities. Colorimetric technologies supply an inexpensive option for prompt and effective threat agent detection, and lend themselves to automation through the incorporation of color imagery or diode transduction.
Interested in A24B-T015 Distributed Multithreat Microsensor? Contact Heather Lange (heather.lange@tetramer.com )
A24B-T018 Biosynthetic PFAS Alternatives to Provide Omniphobicity
Objective: Develop and scale production of biosynthetic materials for environmentally friendly, omniphobic technologies for Department of Defense clothing and equipment without use of fluorine or perfluorinated compounds (PFAS).
Description: The Department of Defense (DoD) uses finishes with perfluorinated compounds (PFAS) to provide essential properties for Warfighter protection and survival, including water, chemical, oil, and stain repellency for clothing and equipment items. PFAS, which are associated with cancer, reproductive health issues, and developmental delays, are being banned from use and manufacture worldwide. There are over 9,000 different PFAS compounds, used since 1940 in clothing, food packing, personal care products, water/stain resistant products, and non-stick cookware (1,2). Since PFAS have worked so well in providing water, liquid, oil, and omniphobicity, they have been the default chemicals used in the textile industry to provide the durable treatments needed to meet DoD clothing and equipment requirements.
The DoD is seeking new, biosynthetic and environmentally friendly non-PFAS technologies for clothing and equipment to impart omniphobicity. No PFAS-free alternative has been developed thus far which can provide the needed level of oil repellency, and while water repellency can be obtained, non-PFAS finishes struggle to meet military durability requirements over the expected life cycle of an item. Truly novel non-PFAS formulations/technologies are needed that can provide durable omniphobicity equivalent to those obtained using PFAS.
Biosynthetic materials are key to sustainable domestic production and offer new opportunities to discover and synthesize novel compounds (3,4). The goal of this topic is to solicit new biosynthetic material technologies that can replace PFAS compounds in DoD clothing and equipment, providing the needed level of oil repellency and durability. The developed non-PFAS bioinspired solution should target at least one of the following areas: textile-based systems clothing and equipment items (uniforms, shelters, sleeping bags, hydration systems), food packaging and/or protective clothing items (barrier materials) and be developed into a formfactor that can be integrated into an end item. The biosynthetic solution may be provided as an alternative coating or finish for an existing DoD item, or as an entirely new material or substrate with inherent repellency to replace and/or be integrated into existing materials within the DoD system. Integration into DoD end items must consider other requirements for the final product, such as retaining water repellency, flame resistant properties, or others.
Specific care must be taken to avoid “regrettable substitutions” such as siloxanes, which are under similar scrutiny as PFAS compounds from health and safety standpoints. Due to health, safety, and regulatory concerns, solutions should not contain any carbon-fluorine bonds, including partially fluorinated fluoropolymers, even those not defined as “PFAS” by the EPA. Thoroughly review state-of-the-art for non-PFAS substitutions and be familiar with environmental concerns for manufacture (such as the use of isocyanates or solvents) as well as feasibility of producing omniphobicity with the proposed system using environmentally friendly materials and processes (5). (Suggested Reference: https://www.ri.se/en/popfree/pfas-substitution-guide-for-textile-supply-chains)
Interested in A24B-T018 Biosynthetic PFAS Alternatives to Provide Omniphobicity? Contact Dr. Monika Mujkic (monika.mujkic@tetramer.com)
A24B-T019 Additive Manufacturing for Protective Eyewear
Objective: Develop materials and an approach to manufacturing ballistic protection eyewear lenses with integrated prescription correction that is also suitable for point-of-need additive manufacturing.
Description: Combat eye protection is a ubiquitous need for all deployed Soldiers. The eyewear provides the wearer protection against ballistic-fragmentation and environmental concerns, like blowing sand, while remaining transparent to retain situational awareness. Protective eyewear lenses are currently made via injection molding and are not easily customized to provide vision correction. Any needed prescription vision correction is currently achieved with the Universal Prescription Lens Carrier (UPLC).[1] The UPLC sits behind the primary protective lens and contains a separate set of corrective lenses specific to the User’s vision correction needs mounted into the UPLC frame. This creates integration issues for equipment worn on the face and eyes and limited field-of-view through the prescription lenses in addition to adding substantial logistical burden. The Army product manager for Soldier Protective Equipment (PdM SPE) has an ongoing initiative to identify technologies that would allow the elimination of a separate vision corrective lens (I.e. an integrated vision correction / ballistic protection lens). These lenses are expected to have a life cycle of less than six months since ballistic eye protection lenses are often rapidly degraded in combat environments due to scratching and abrasion.[2] Therefore, it is also desirable to have rapid turnaround on individually customized corrective lenses and to limit the logistics burden by providing manufacturing capability that is close to the point-of-need as well as being customizable to an individual wearer. An additive manufacturing (AM) method is most likely to meet these requirements. As AM technology has progressed, printing resolution and material development have improved to the point where optically clear samples are now achievable.[3] The cost of this technology has also decreased to being a commercially viable approach to manufacturing custom lenses. Companies in this space are continuously developing new materials for their 3D printers to impart performance that has only previously been attainable with conventional manufacturing methods. Significantly, the expanded use of augmented reality (AR) in both military and civilian sectors has spurred advances in optically clear and durable eyewear manufactured with AM.
The goal of this topic is to develop materials and processes to rapidly manufacture a customized (“one off”) optical lens that meets all requirements of MIL-PRF-32432A for ballistic protection lenses as well as providing excellent optical quality, dimensional tolerances, and stability in all environments sufficient to provide vision correction.
Interested in A24B-T019 Additive Manufacturing for Protective Eyewear? Contact Adam Haldeman (adam.haldeman@tetramer.com)
Contact us to learn how to initiate collaborations with Tetramer.
Tetramer Operational Infrastructure to support this work includes:
-
DCAA approved accounting system
-
NIST SP 800-171 and CMMC 2.0 Level 2 cybersecurity program
-
Facilities Security Officer
With expertise in research (TRL 1-4), product development (TRL 5-6), scale-up (TRL 7-8), and manufacturing (TRL 9), Tetramer supports the entire innovation process.
TRL
1-2
Ideation
TRL
3-4
Feasibility
TRL
5-6
Development
TRL
7-8
Scale Up
TRL
9
Mission Proven
Click the stages above to see how Tetramer can help advance technologies from lab to market.
Previous Defense & Energy Partners
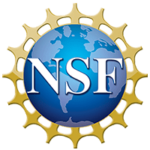
National Science Foundation
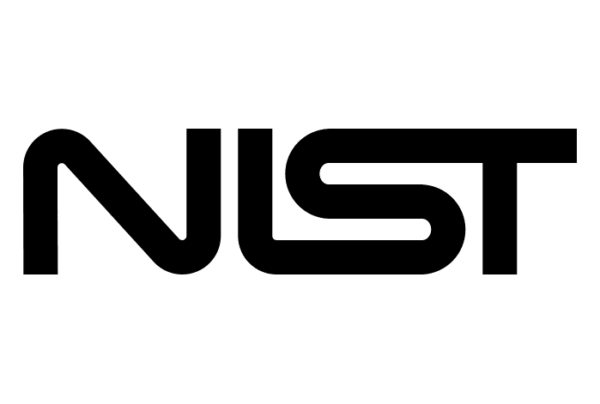
National Institute of Standards
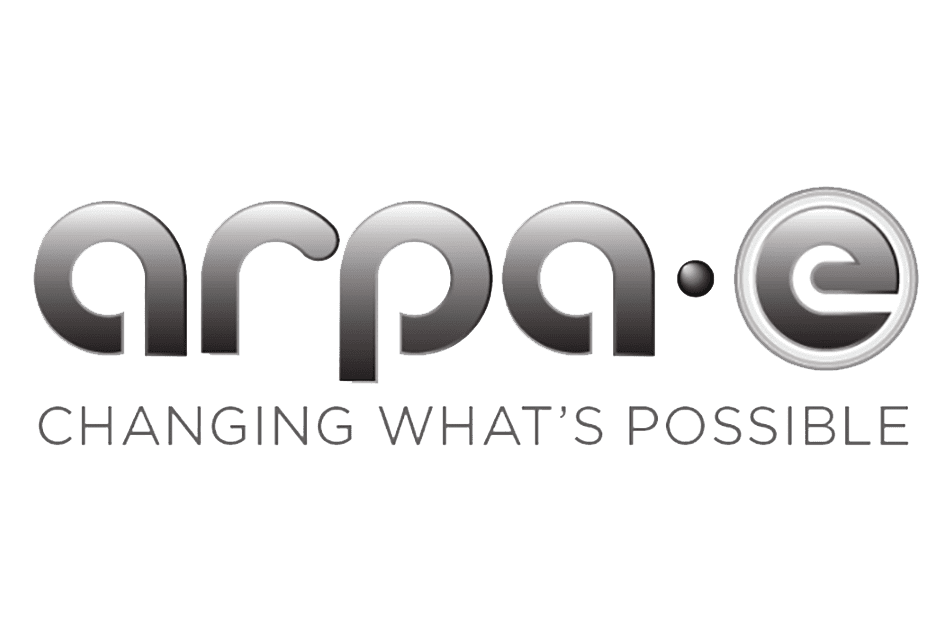
Advanced Research Projects Agency - Energy
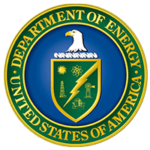
Department of Energy
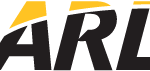
Army Research Laboratory
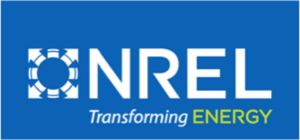
National Renewable Energy Laboratory
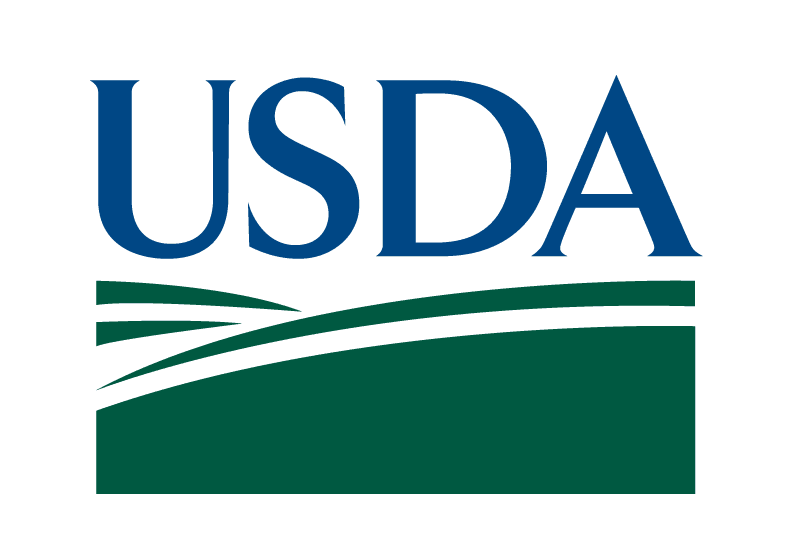
Department of Agriculture
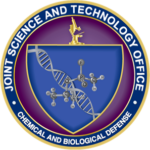
Joint Science and Technology Office for Chemical and Biological Defense
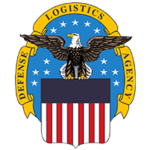
Defense Logistics Agency
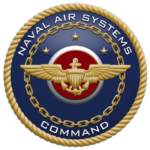
Naval Air Systems Command
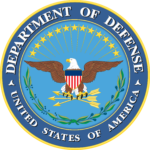
Department of Defense
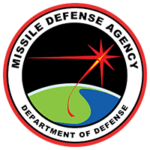
Missile Defense Agency
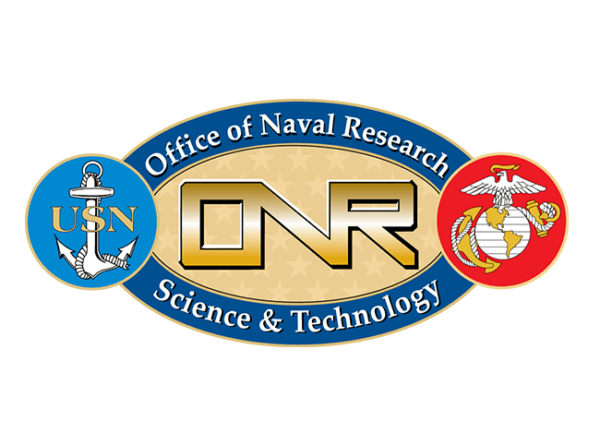
Office of Naval Reseach
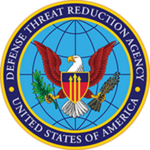