This is part of a series of posts to share more about the services Tetramer offers and the types of customers we serve.
When industry leading customers, like Techtronic Industries (TTI) encounter issues with materials quality or performances they reach out to Tetramer Analytical Services . We have the expertise and equipment in house to help identify, communicate, and solve materials challenges. We partner with our customers to understand all of the constraints surrounding the issue and then work to find the best solution.
TTI is located just a few miles from the Tetramer facility and manufactures brands including Milwaukee®, Ryobi®, Dirt Devil®, Homelite®, Oreck®, and Hoover® among others. As a fast-growing world leader in Power Tools, Accessories, Hand Tools, Outdoor Power Equipment, and Floorcare, TTI is at the cutting edge for Do-It-Yourself (DIY), professional, and industrial users in the home improvement, repair, maintenance, construction, and infrastructure industries.
In order to ensure that their products are of the highest quality, TTI brought some plastic parts for one of their products to Tetramer. The team worked with TTI to clearly understand and investigate the root cause of the problems. John Earl, Director of Engineering, said this about working with Tetramer:
"So far, I would characterize our analytical experience with Tetramer as very good. We have worked we many test labs (domestically & internationally). We’ve had you guys do several different types of analysis for us recently on a high priority project (TGA, DMA, FTIR, DSC, TGA/Mass Spec, TGA/DSC/Mass Spec, TMA, XPS- Elemental Analysis) to help isolate some potential issues with plastic parts in one of our assemblies. At the onset of the project, we had only a few different theories as to why we may be encountering the functional issue with the assembly, and worked together through several rounds of testing, PPTs, and several in-depth conversations to help us get a fundamental understanding of the root cause of our projects problem. There are many companies that have technical test capabilities and expensive machines but can’t follow through to help educate a customer through a transparent exchange of ideas. I think this really sets your team apart from other companies we’ve worked with. I’ve found the recent project interesting, engaging, and quite honestly, a fun learning experience."
John Earl, Director of Engineering, TTI
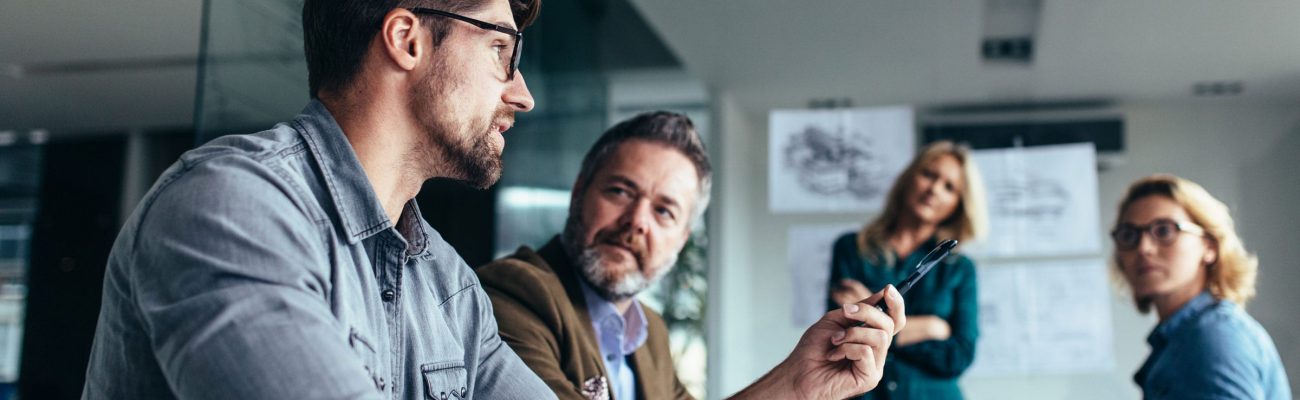